Traditional Skills
Buchanan’s clocks are 100% handmade. To do this there are countless unique and special skills required and this is very important to Buchanan. It is what makes our clocks stand out from any other clock made today. Anyone can purchase a machine or a tool, but it takes a particular dedication and focus to learn and refine the skills that are needed to use them and achieve results. For our readers interest we put below some of the traditional skills and methods used in the creation of our timepieces.
Fine Wheels
Each gear in a Buchanan clock is a different size. They also have different numbers of teeth and different sizes of teeth. A formula is used to determine the thickness of the spokes compared to the thickness of the rim. Once this known the blank which has its teeth already cut is placed on a special purpose jig and the spokes are scribed onto the metal. Next, holes are drilled through in the waste section of the gear. This allows the saw blade to be passed through the material and then with skill guided along the scribe lines to cut out the waste, leaving thin spokes in place. Once this is done the wheel is finished by hand using fine files. Any variance in the cutting is removed with the file and the last of the waste material removed to the scribe lines. Special attention is taken to make sure that the corners where the spoke joins the rim or the centre are a perfect intersection. To make sure the centre hub of the wheel is the correct size and shape, a set of steel “buttons” are made which fit through the centre hole of the wheel. These are then clamped carefully in the bench vice and give a guide when filing the wheel centre to shape.
Jewel Cutting & Polishing
Buchanan cuts and polishes their own jewels for use in their clocks. These jewels are placed in positions where they work as a bearing surface where low wear is essential. This allows Buchanan’s clocks will run for many years with low maintenance and a lifespan of hundreds of years. Raw Ruby is cut on a diamond saw to aas close as possible to the final shape. Then the jewel is mounted on a purpose built polishing machine. Different grades of diamond impregnated wheels are used on this machine and the jewel is lowered onto the spinning wheel and moved back and forward. A Vernier gauge used to determine the final dimension of the jewel.
Hand polishing
Once the clock is mechanically complete Buchanan takes pride in finishing each component to a degree that is rarely seen in clock making. This requires hours of time spent in hand polishing each component. The finest details are taken into account. Parts that are rarely, if ever, seen get the same attention. Buchanan believes that by taking attention to the smallest details which one might think are not noticed, combined, lead to the complete timepiece having the depth of quality that is so important to a masterpiece.
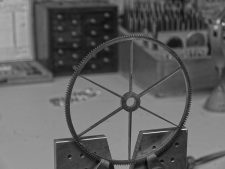
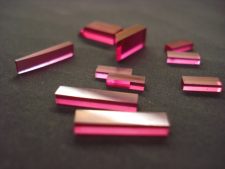
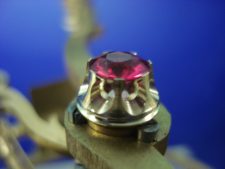
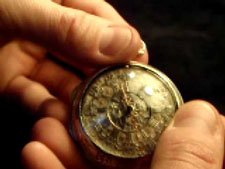